Composite laminates or pre-pregs typically consist of a resin and fabric, often with woven yarns supporting and encapsulating the resin matrix – the fabric is considered the base substrate of the composite. The final material exhibits a combination of properties that is better than the properties individually exhibited by the constituent materials. As a result, a composite material’s functional and aesthetic characteristics will vary significantly depending on the fabric and resin used. For this reason, it is important to choose both components carefully to ensure the performance in the intended application.
The following guide discusses some of the key considerations to keep in mind when selecting a fabric. As composite manufacturers generally use fabrics rather than individual fibers during material manufacturing operations to facilitate handling, it covers design factors such as fiber type, woven vs. non-woven, weave pattern, weight, thickness, and finish. The article also highlights the general advantages and typical applications for woven fabrics.
Design Considerations for Selecting Fabrics
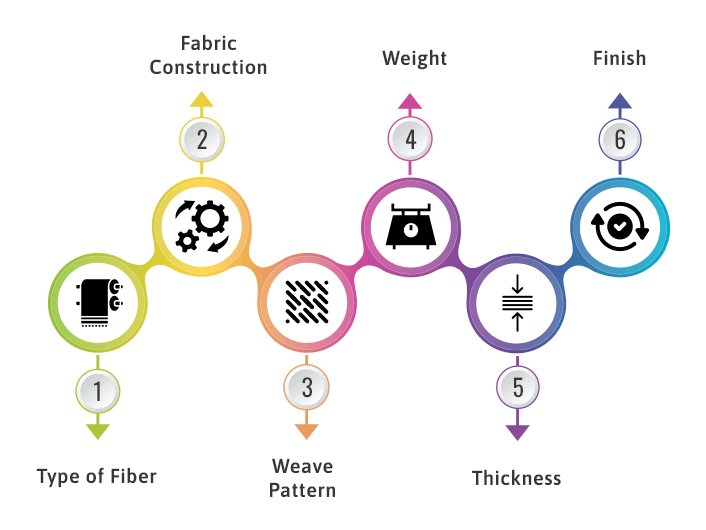
There are many factors to consider when choosing a composite material. Below we outline some of the most important ones.
Type of Fiber
Composite manufacturers utilize a wide range of fabrics in their materials to achieve different end material properties for different applications. Some of the most commonly used fabrics for composite applications include:
- Glass. Glass fabrics offer excellent shear strength, thermal stability, and electrical insulation at a low cost. The most common types of fabrics include S-glass and E-glass. S-glass has higher strength, impact resistance, stiffness, and temperature resistance than E-glass. While E-glass offers slightly lower performance on these metrics, it is more cost-effective and features excellent electrical and thermal insulation properties.
- Aramid. Aramid fabrics are low-density materials that offer exceptional impact strength, fire resistance, and thermal insulation properties.
While the above fabrics are widely used for the manufacture of composites, composite materials manufacturers may also use other fabrics depending on the application. For example:
- They use boron to coat carbon/metal fibers to enhance performance. However, the high cost of boron-coated fibers limits their use to critical applications (e.g., aerospace) or highly specialized applications (e.g., specialty sporting equipment).
- They use ceramic fibers for composite materials that need higher temperature resistance.
- They use natural fibers in low-tech applications.
- They use polyester fibers to reduce material weight, increase impact and/or abrasion resistance, and lower production costs.
- They use quartz fibers for advanced applications that require low dielectrics, high strength and superior thermal resistance (up to and exceeding 1000° C).
Fabric Construction
Fabrics can be classified into woven and non-woven variations. Woven fabrics feature a tight warp-weft pattern that makes them difficult to separate. Non-woven fabrics feature an interconnected fiber matrix bound together by chemical or thermal methods. While woven fabrics generally offer greater strength than non-woven fabrics, the latter varies in durability depending on the fibers and coatings used.
Fabrics can also be categorized into unidirectional and bidirectional variations. Unidirectional fabrics have all of their fibers oriented in the same direction. As a result, they provide composite materials with the maximum possible strength and stiffness for the particular fiber material in that direction. Bidirectional fabrics have fibers oriented in two directions, which are perpendicular to one another. As a result, they provide strength and stiffness in both directions.
Weave Pattern
Woven fabrics come in a number of different weave patterns, each of which influences the material’s stiffness or drapability and thickness. For composites, fabrics most commonly feature the following patterns: Plain-weave, Basket, Leno, Four Harness Satin, Eight Harness Satin, and Twill. Plain-weave fabrics are the most stable, while the eight harness satin fabrics allow for the greatest degree of drapability.
Weight and Thickness
The weight and the thickness of the fabric depend on the weight and thickness of the fibers. For glass fabrics, weight typically ranges between 0.50 osy to 52 osy (17 gsm to 1,773 gsm), and thickness typically ranges from 0.001 inches to 0.060 inches. The unit “osy” stands for ounces per square yard while the term “gsm” stands for grams per square meter.
Finish
The finish of a glass fabric refers to the chemical application on its surface applied post weaving that is designed to perform in the intended downstream application.
Advantages of Composite Materials
Composite materials offer many advantages to customers when designed and constructed properly. Some of the key advantages include:
- Broader design flexibility. Composite materials are available with a variety of polymer and fiber options, which makes it easier and simple for customers to choose the material that best suits their needs. Additionally, the resulting material can be engineered to take on nearly any shape or form.
- Greater productivity. A cleverly designed composite product can combine multiple manufacturing steps into one, streamlining the production process and saving time and money.
- Better durability. Composite materials are generally strong and durable. Additionally, they offer varying levels of resistance to chemicals, corrosion, heat/flame, smoke, and toxicity. Customers can select the material with the characteristics that meet their application requirements and restrictions, ensuring the finished component performs as intended.
- Higher strength-to-weight ratio. Compared to other materials, composites have an excellent strength-to-weight ratio. The combination of polymer and fiber results in strength and durability comparable to metals with a fraction of the material weight.
- Excellent dimensional stability. Composites are suitable for components that require high dimensional accuracy as they carry low post-mold shrinkage risk.
Applications of Composite Materials
Composite materials find application in a wide range of industries, including, but not limited to, the following:
- In the aerospace industry, composites materials are used for components of aircraft and satellites, such as structural supports, gaskets, interior elements, and cargo liners.
- In the ballistics industry, composite materials are utilized in a variety of safety and protection applications. Some of the most common types include para-aramid materials such as Kevlar® and Twaron® and UHMW polyethylene materials such as Dyneema® and Spectra®.
- In the electronics industry, composite materials are used as the base substrate for printed circuit boards (PCBs) for the communications, aerospace, automotive, military/defense, and other industries.
- In the power industry, composites are used as insulating components for power generation and management equipment.
- In the food service and industrial belting industry, composites are used for food processing, cooking, baking, and preparation as well as packaging applications.
- In the recreational industry, composites materials are employed in the construction of various pieces of equipment, such as surf and snowboards, race cars, bicycles, bats, hockey sticks, and other sports gear.
Quality Composite Materials by JPS
At JPS Composites Materials, we are the leading manufacturer of high-strength composite reinforcement fabrics. If you’re looking for a composite material, we’ve got you covered. We offer a broad selection of fabrics to suit many applications, including reinforcing, sound and thermal insulation, and ballistic protection. By partnering with us, you benefit from our experts, who have the knowledge and skills to help you find the right product for your needs.
Our material offerings include:
- Glass: E-Glass, S2® Glass, T-Glass, and L-Glass®
- Quartz: Astroquartz®
- Para-aramid: Kevlar® by Dupont and Twaron® by Teijin
- UHMWPE: Dyneema® by DSM and Spectra® by Honeywell
In addition to manufacturing fabrics, our team continually looks for new and novel materials to use. We can weave thermoplastics, basalt, and other non-traditional reinforcement materials in non-traditional patterns.
All of our fabrics are designed and constructed to meet industry specifications and standards for a wide range of applications. The specifications and standards we manufacture toward include AMS, ASTM, BMS, IPC, and Mil-spec.
As the North American leader in the high-performance woven glass and aramid industry, JPS has a 50+ year history and commitment to servicing advanced composite applications with fabrics that meet customers’ diverse and challenging needs.
For more information about our composite materials or assistance choosing one for your application, contact us today.